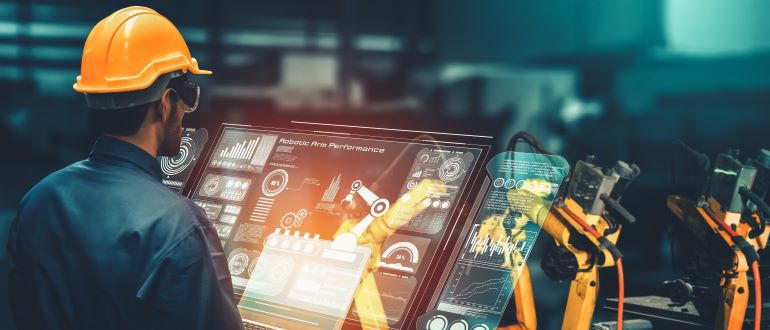
Artificial intelligence can be an incredibly powerful tool for training in manufacturing because it allows for virtual simulation, customized programs and performance tracking and feedback. Based on the most likely situations workers will face in their roles, AI can take many variables and create more true life scenarios from the simple to very complex, whether around plant conditions, machine maintenance and repair, standard work or material considerations.
These AI inputs can even involve real-time performance indicators or equipment readings to allow a worker to practice tasks or skills ranging from those used frequently to complex problem solving and teamwork skills needed to address the most challenging potential scenarios.
Detroit-based startup DeepHow sees an opportunity to use AI to accelerate skills training for shopfloor and other highly technical skilled trades workers. The company’s system captures know-how and manual skills, then uses AI, natural-language processing, computer vision, and knowledge mapping to convert this knowledge into how-to training videos.
DeepHow’s AI Stephanie platform analyzes a video of a skilled worker performing a complex task, identifies the steps involved and then creates a step-by-step training video.
Sam Zheng, co-founder and CEO of DeepHow explains creating video training content has traditionally been costly and time-consuming.
“However, when you apply AI to create video training content, it dramatically scales your video creation operations, making it easy to streamline content creation and build new training videos — without the need to hire expensive film crews or staff up with video content specialists,” he says.
With one click, AI adds advanced features such as transcribing and translating video content, enabling specialized skills know-how to be captured and shared with anyone in a multilingual workplace or across different countries.
“Another bonus is that you don’t need a professional videographer to segment content into chapters, add headings or annotations, or add subtitles; let the AI do it all for you,” he says.
Zheng points out today’s learners aren’t turning to PDFs and manuals; they look for YouTube and video resources to watch someone physically perform a task and then emulate that person’s methods and techniques.
“In industrial settings, organizations that leverage AI-powered tools to create training videos can tailor the experience to their employees’ specific learning needs,” he adds.
For example, if specialized keywords or methodologies resonate with an audience, AI-powered tools can help trainers take advantage of that. Another consideration is accessibility: AI makes training accessible for workers regardless of their primary language and can make video training accessible for hard-of-hearing or deaf employees — addressing workplace policies and legal mandates.
“The ability to personalize training for each worker’s training or performance is one of the more compelling AI applications in manufacturing,” explains Claudia Saran, KPMG’s national industrial manufacturing sector leader.
She notes AI can generate real-time insights around performance and build training or coaching that targets those areas of development while also providing the worker key feedback in the process.
“The personalized training, for example, can vary by topic and by the depth of information covered,” Saran adds.
She calls the ability to personalize training for each worker’s training or performance is one of the more compelling AI applications in manufacturing.
“AI complements other forms of training and development and does not take the place of traditional training methods by teammates, supervisors, and plant managers,” Saran says. “It can be a great addition to the workforce training toolkit, but also requires careful monitoring and significant input to be impactful.”
Zheng adds one of the hardest–but perhaps most valuable–benefit of using AI-powered training tools is the ability to pass on “know-how”.
“Senior, experienced workers develop and acquire specialized techniques that make their jobs faster, safer, and more efficient,” he says. “This personal knowledge can be captured and passed on to other workers, contributing to an organization’s overall competitiveness.”