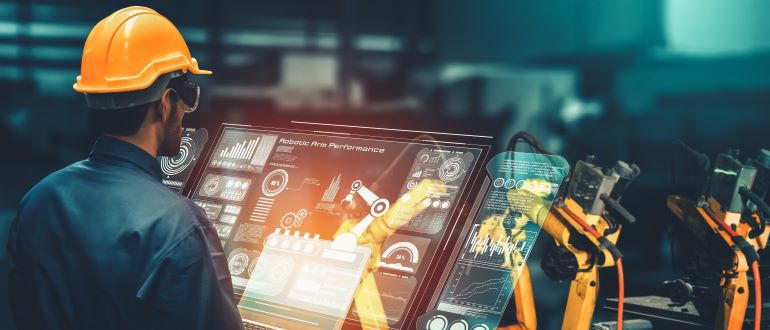
In the mid-18th century, mechanization reshaped manufacturing, permanently altering the course of history. The industry has evolved exponentially since then, moving from electrification to robotics in the blink of an eye. The sixth industrial revolution is already approaching, leaving manufacturers wondering what the future holds — and whether they are prepared.
Fusing IoT and AI Could Revolutionize Manufacturing
Industry leaders are right to believe internet of things (IoT) and artificial intelligence (AI) will transform the manufacturing sector. Deloitte anticipates that digital transformation in manufacturing will likely redefine work for humans, permanently altering how they train and communicate. Based on this prediction, it is only a matter of time before every facility deploys these technologies.
While both IoT and AI solutions enable real-time quality control, they perform considerably better when combined. A machine learning (ML) algorithm can analyze information generated from optical, current, infrared and proximity sensors to determine whether appearance, weight and dimensions align with predetermined specifications. It can also detect defects.
These technologies enable predictive maintenance. Using an ML model to analyze IoT-generated equipment information can minimize unplanned downtime, lowering costs and streamlining repairs. This strategy is effective because even something seemingly minor — such as an anomalous vibration — can signal a loose component or broken part. Automated solutions can detect potential faults long before any human could.
Granularity is vital when dealing with complex machinery in a sector where downtime can cost millions of dollars. However, technicians cannot manually analyze the vast amounts of data internet-connected nodes generate. An algorithm is essential for efficiency and accuracy.
Adaptive production scheduling is another potentially transformative outcome of combining IoT sensors with advanced algorithms. Dynamic, immediate shifts in production to accommodate changes in supply and demand would revolutionize inventory management and allow companies to quickly pivot during supply chain disruptions.
Technical and Security Considerations Before Implementation
Location is the first — and arguably most important — technical consideration. Decision-makers must determine whether to deploy their system at the edge or in the cloud. While cloud-based deployment reduces total maintenance expenses, edge computing can accelerate analysis. Upkeep costs, storage accessibility and vendor lock-in are other factors to consider.
Strategic data integration is vital wherever the system is based at the edge or in the cloud. An advanced algorithm is nothing without high-quality information. Manufacturers must filter out noise, eliminate outliers and audit logic to optimize performance.
Having a human in the loop may streamline this process. A knowledgeable AI engineer can monitor and tweak model performance as needed. Even if the system is mostly or fully automated, a human expert is essential. They may not handle repetitive tasks but can use creativity and critical thinking to solve unexpected issues.
Hiring an expert — or even a team of professionals — is cost-effective at scale because this technology is affordable. McKinsey & Company reports that the unit price of industrial IoT sensors is less than 50 cents, and the cost to store 1 gigabyte of data is as low as 2 cents, demonstrating the affordability of this approach.
That said, developing an in-house ML system is more expensive. Development can cost anywhere from $10,000 to $9,000,000 — depending on project scope. Manufacturers may have to use a third-party vendor’s product to stay within budget. However, that could introduce cybersecurity issues. Network segmentation, authentication and ongoing audits being vital, training and upskilling can help bring technicians up to speed.
Could IoT and AI Revolutionize the Manufacturing Industry?
It has been decades since robotics transformed manufacturing. While strides have been made with data storage and automation technologies, nothing has come close to having the same impact — until now. Industry professionals could use IoT and AI to transform everything from hiring to task completion, permanently changing core sector functions.