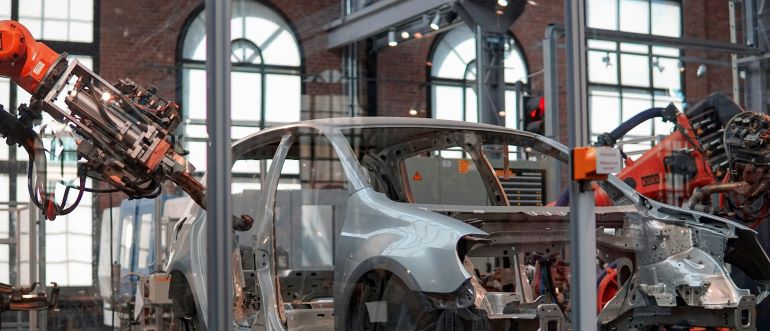
Canadian company Vention, which claims to offer the only end-to-end platform to design, automate, order, deploy and operate automated equipment and robot cells in the cloud, has added AI into its design process, to create more intuitive and smarter robotic arms, and all adjacent devices in a robotic cell. This new capability is available to over 4,000 manufacturing clients who currently use Vention.
“Unlike traditional 3D design and offline programming software, Vention’s Manufacturing Automation Platform (MAP) is poised to leverage AI to simplify the design-to-deployment experience,” said Etienne Lacroix, Vention’s founder and chief executive officer. “With a dataset comprising over 365,000 automated equipment and robotic cell designs, each labeled with rich geometric data and metadata, and continuous investment in Vention’s Geometric Reasoning Engine and Graph Neural Networks, the task of designing, automating, ordering, deploying, and operating robotic cells in the cloud has never been more seamless. And this is just the beginning.”
Vention shares that key features include a “Refined design flow, smarter part placement, and enhanced part manipulation.”
“The new quick-start feature lets manufacturers start a project from scratch or choose from Vention’s extensive design library, providing flexibility based on need, knowledge, and time. When users are creating their own design or customizing one from the library, the new AI-driven Geometric Reasoning Engine (GRE) helps them place components correctly. This makes cell design accessible even to non-technical builders. Plus, the enhanced 3D interface makes for intuitive part manipulation, with seamless part moving and automatic snapping. A standout feature is a real-time view of the bill of materials, pricing, and part specifications, which offers instant visibility into project essentials. Tech specs, 2D drawings, and more are now directly available in the 3D design environment.”
Mr. Lacroix said the company has come a long way since it launched in 2017, when it carried only 70 industrial components, mostly for carts, pedestals and workstations. Now the company offers thousands of parts, and categories such as robotics, sensing, conveyor systems, motors, gearboxes and more, Mr. Lacroix said. Vention has approximately 300 employees and serves over 4,000 customers, representing over 25 industries, throughout five continents.
The company’s unique structure helps manufacturers automate their production floors in just days, through a “democratized user experience.” MAP allows for designing, automation, deployment and operation of automated equipment directly from their web browser.
Mr. Lacroix spoke this week, on May 6, 2024, at the Automate 2024 Conference in Chicago. The week-long conference features over 800 exhibitors. His topic was “The Rise of the Advanced Manufacturing Team and DIY Industrial Automation.
He said that industrial automation has undergone relatively few changes in the past 30 years, and was not typically designed for the medium- to smaller-sized businesses, but to “high-throughput manufacturing.”
“This left small and medium-sized businesses, the ones who would benefit from the democratization of automation, behind,” Mr. Lacroix said. “Over the past year, Vention has done extensive research on the impact that recent innovations, specifically the platforming of industrial automation, have had on the industry. We found that small and medium-sized businesses that were previously hindered by capital investment barriers are now leading the charge in adopting the Manufacturing Automation Platform and do-it-yourself (DIY) automation because of their accessibility and low barrier to entry. The result? More manufacturers are leveraging their internal resources to create the Advanced Manufacturing Team.”
Siemens, the world’s largest provider of industrial automation, is continually looking into ways to integrate AI into its massive catalogue of products.
“In today’s manufacturing, robots deployed across various industries are mostly doing repetitive tasks. The robots’ overall task performance hinges on the accuracy of their controllers to track predefined motions. The ability of robots to handle unconstructed, complex environments, such as the flexible grasping of previously unknown objects or the assembly of new components, is very limited. Endowing machines with greater levels of intelligence to acquire skills autonomously and to generalize unseen situations would be a game-changer for quite a few industry sectors,” according to Siemens.